CNC mills are revolutionizing how manufacturing workshops operate. They have increased their production capacity, improved quality, and eliminated waste production – all at the same time. However, high-speed and high-volume machining may generate heat that can impede its performance. And this is where a coolant enters the picture.
In this post, we will be examining how a coolant adds value to tabletop CNC and the various delivery channels for the same.
The Role of a Coolant in CNC Machining
At first glance, the role of a coolant in CNC machining may appear pretty straightforward – to leave behind a cooling effect. However, it plays a rather compounded role, which can be broken down into three primary actions:
1. To Cool
Interestingly, cooling is the least vital role of the CNC coolant. However, it does play a role in transferring heat from the site where the machining takes place so that the tools or feed do not overheat.
Liquids are more effective in regulating temperatures than air. However, water-based coolants are found to be more effective at heat transfer than oil-based coolants.
2. To Lubricate
Certain metals that have a low melting point tend to melt and adhere to the CNC milling tools. At the same time, the heat generated due to the friction between the machine tool and the feed contributes to this inadvertent welding.
In such a scenario, CNC coolants can serve as lube that prevents the “sticking” of metals with each other due to accidental heat treatment. It also renders the debris less likely to adhere to equipment surfaces.
3. To Clear
Clearing up waste, chips, and debris is one of the most crucial roles of CNC coolants. Spraying the coolant onto the region where machining takes place gets rid of any waste that may come into the field of the cutter. This act also minimizes recutting and offers an impressive finish to the products.
Overview of the Different Types of CNC Coolant Delivery Systems
Now that you know the primary reasons behind using CNC coolants, let’s take a look at the different delivery systems. Based on the pressure, delivery action, or coolant type, the CNC coolant delivery models can be broadly categorized as:
1. Flooding System
As the name suggests, in this system, large volumes of the coolant are streamed onto the tools, workpiece, and machine. It is a low-pressure delivery system that removes chips, prevents recutting, dissipates heat, and adds lubrication.
2. Misting System
Misting is yet another low-pressure coolant delivery system that releases the fluid in its atomized form. These tiny particles of the coolant produce a mist or a fog that settles onto the machine and the workpiece.
It is commonly used where chip evacuation and heating are not a pressing requirement. In other words, it is an effective lubricant for high-speed applications.
3. Air Coolant System
For the air coolant delivery systems, a stream of air is released into the workspace and onto the workpiece. Given that air is not a lubricant, this delivery channel is primarily used for clearing chips and cooling the section.
Even though air may not be one of the best coolants for heat transfer, it is one of the most inert ones, making it less likely to react with the workpiece even upon direct contact.
Air coolant delivery is majorly used while machining plastics as direct coolant application can cause rapid contraction or thermal shocks.
4. Jetting System
As the name indicates, the jetting system releases the coolant liquid at pressures that are as high as 1,000 psi on average. It is mainly used for its chip-clearing action as high-pressure jets can efficiently blast away the chips from the workpieces.
However, it also bears a modicum of risk as jetting pressures can damage delicate jobs and even miniature-diameter tooling. As a result, it is often used in drilling operations with delivery via tooling.
5. Minimum Quantity Lubricant
Minimum Quantity Lubricant, or MQL, is also known as micro lubrication or near-dry machining. It is one of the most well-known coolant delivery systems that is used by workshops for its cost and performance efficiency.
MQL involves a blast of cooling air, followed by the delivery of an extremely fine mist or an aerosol, to offer lubrication.
As a result, the coolant can deliver lubricity, sufficient cooling, and chip evacuation while supporting machine operation without wasting resources. Resultantly, it also brings with it the environmental benefit of waste reduction, which is another point in its favor.
Which Coolant Delivery System Is Best for Your Project?
We have enlisted various coolant delivery systems in CNC machining with their unique characteristics and capabilities. With the above knowledge, you can make an informed decision on the nature of the coolant delivery system that can serve its purpose.
However, you will have to carry out routine and regular maintenance to ensure that coolants and the delivery systems deliver to expectations.
This is a guest post By Peter Jacobs From the CNCMasters team
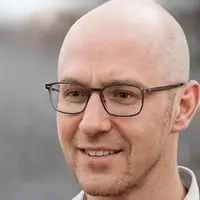
Peter Jacobs is the Senior Director of Marketing at CNC Masters. He is actively involved in manufacturing processes and regularly contributes his insights for various blogs in CNC machining, 3D printing, rapid tooling, injection molding, metal casting, and manufacturing in general knowledge.